3D打印作为第四次工业革命的典型技术,正在赋能产品设计的自由度,也为热交换器这样的产品带来了产品创新的新空间,根据3D科学谷的市场观察,HamiltonSundstrand通过3D打印提升了陶瓷逆流热交换器热效率。
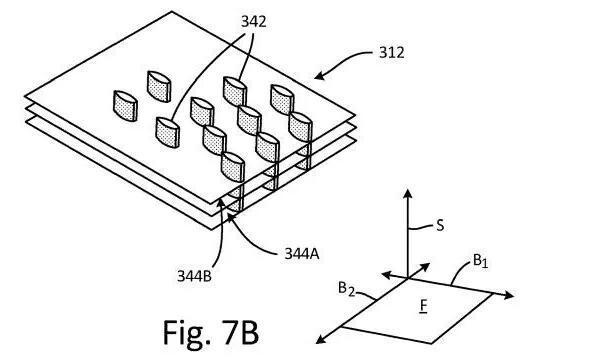
为3D打印技术特点而重新设计
典型的板翅式热交换器通过热空气和冷空气通过通道以便交换热量。在燃气轮机叶盘冷却系统中,热空气来自发动机压缩机,冷空气流过发动机风扇管道。
热通道和冷通道是相似的,并且每个通道包括一排冷却翅片或闭合杆,它们定位在分隔板上以限定每个通道。典型的热交换器具有翅片,以限定交替的热通道和冷通道。组件被放入真空炉中进行钎焊。在钎焊过程中,挤压叠层以迫使片材和翅片在一起。
不过当温度超过常规金属(例如,低温材料)的耐温范围时,就需要高温热交换器,并且可能需要紧凑的热交换器。例如飞机发动机预冷器,燃气电厂回热器和固体氧化物燃料电池废热回收等,这些都在高温范围内(T> 800°C) )。
目前广泛使用的金属材料,可承受高达700°C的温度。包括金属超合金,例如不锈钢,Inconel和Haynes合金。而陶瓷热交换器技术提供了满足高温要求的解决方案,可允许入口温度高达900.degree。不过陶瓷热交换器仍然存在制造限制。
Hamilton Sundstrand (UTC联合技术的子公司)通过逐层增材制造技术来构建陶瓷高温板翅式逆流热交换器。根据3D科学谷的市场研究,Hamilton Sundstrand采用的是层叠对象制造(LOM)过程。通过在垂直于板堆叠方向(即,沿逆流平面)的方向上堆叠层压带来完成,以形成生坯组件,然后将其烧制以形成整体式陶瓷热交换器。
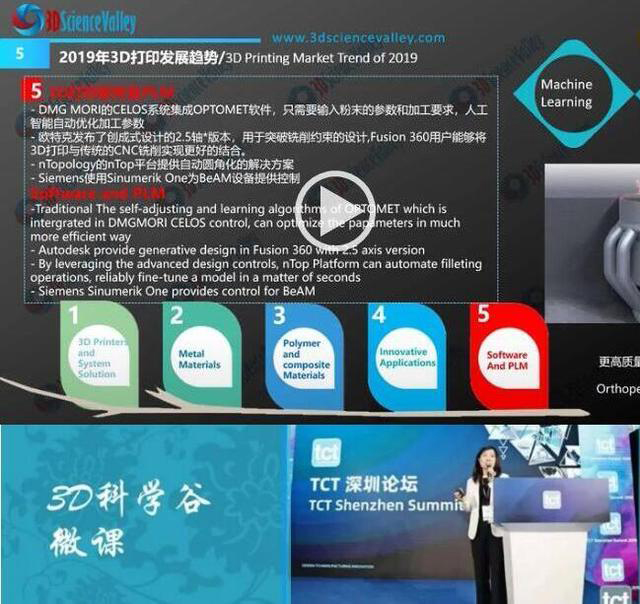
为3D打印技术而设计的结构。来源:US10415901B2
在现有的逆流热交换器中,全陶瓷设计在垂直(即板堆叠)构建方向上通过增材制造LOM工艺是不可制造的。由于制造歧管所需的复杂几何形状,包括难以处理每个带层中的细长条带和有效地提供与各个逆流通道之间的连接所需的相对宽的开口。因此,垂直构造的逆流芯的歧管必须与芯分开制造,然后机械连接。这产生了材料界面(例如,金属/陶瓷界面),产生不希望的热膨胀和收缩差异。此外,高导热陶瓷的机械加工本身是困难且昂贵的。
根据3D科学谷的市场研究,Hamilton Sundstrand通过添加支撑轴向翅片的横向翅片,构建了根据LOM工艺构造的横流式热交换器。为了消除整个组件中的显着的材料差异和机械界面,第一歧管和第二歧管组件可以整体地形成。
3D科学谷Review
根据3D科学谷的市场研究,另外一家公司诺思罗普·格鲁曼公司(Northrop Gramman Systems)开发了一种创新设计的热交换器,特点是外部管道的极大简化,但是这种创新设计的热交换器通过传统制造技术难以构建。特别是连接部位的钎焊或焊接是困难的,尤其是考虑到所涉及的材料非常薄,尺寸非常小,并且接缝都必须防漏。然而,通过增材制造技术(也称为3D打印)很容易构建这些结构。增材制造不仅可以替代钎焊或焊接过程,还可以通过增材制造来构造热交换器通道矩阵,在需要大量集管的情况下,通过增材制造来构造整个热交换器组件 – 包括所有集管成为有效的制造方式。3D科学谷了解到这其中值得注意的是,通过增材制造,通道不必是直的,整个热交换器几乎可以呈现任何形状 – 包括弯曲,扭曲,翘曲等形状。
增材制造技术能够制造逆流热交换器中的交替通道,而对于传统制造技术来说这基本是不可能实现的。交替通道的逆流设计提供最大的热交换器效率,这使得热交换器的尺寸和质量最小化,并且流体流速降低。
总之,3D打印开启了高性能组件的制造新的可能。而在3D科学谷看来,热交换器的3D打印目前还处在起步阶段,这个领域的未来充满了可能性。3D打印的应用可以使工程师有更多的自由度实现设计要求,突破传统的加工方式的束缚,为当前的零件制造带来颠覆性的改变。
3D科学谷将在本周发布的《3D打印与换热器及散热器应用2.0》-下篇,分享国内外机构在3D打印散热器、热交换器领域代表性知识产权、软件,换/散热器设计、仿真与优化,激光考虑,材料考虑,后处理考虑,敬请关注。